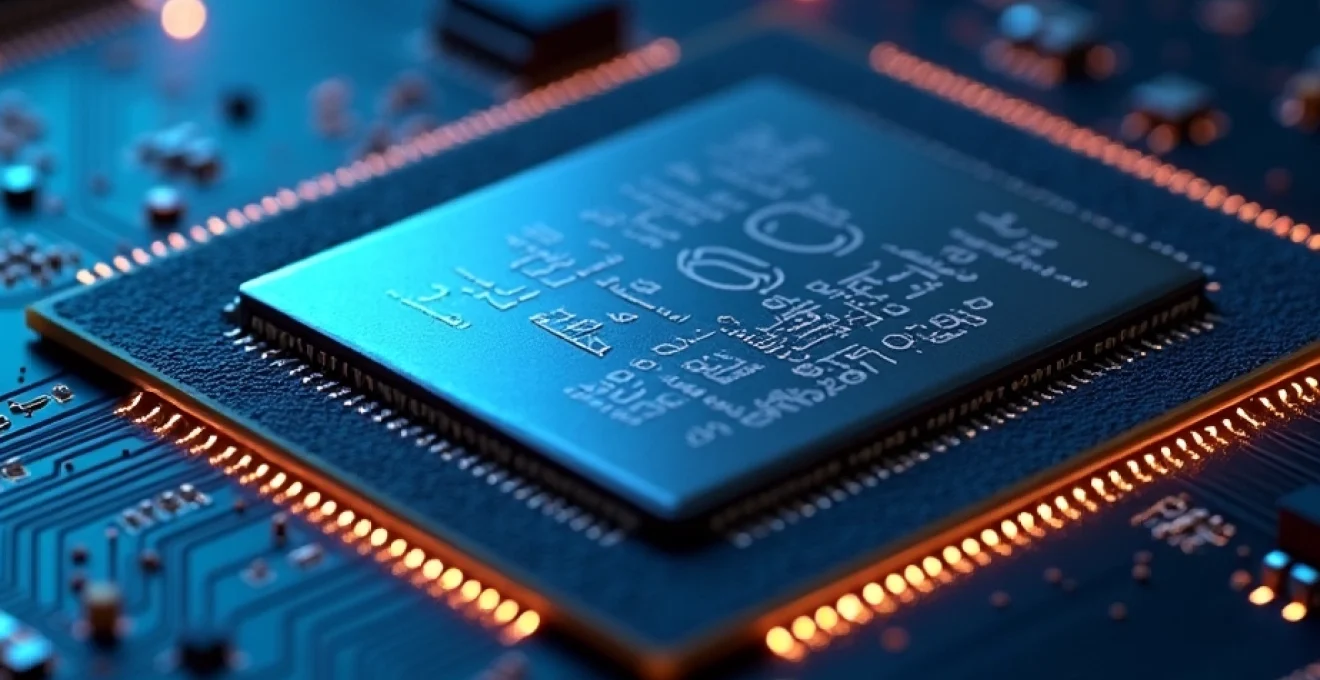
Printed Circuit Board (PCB) technology forms the backbone of modern electronics, enabling the creation of compact, efficient, and reliable devices that power our digital world. From smartphones and laptops to advanced medical equipment and automotive systems, PCBs play a crucial role in connecting and supporting electronic components. As devices become smaller and more powerful, the importance of PCB technology continues to grow, driving innovation across industries.
PCB technology enables compact electronic designs
One of the primary reasons PCB technology is essential in modern electronics is its ability to facilitate compact designs. As consumer demand for smaller, more portable devices increases, manufacturers rely on advanced PCB designs to pack more functionality into less space. This miniaturization trend has revolutionized industries ranging from consumer electronics to aerospace.Multilayer PCBs increase component density
Multilayer PCBs are a game-changer in modern electronics design. By stacking multiple layers of circuitry, these boards allow for significantly higher component density compared to single or double-layer boards. This increased density is crucial for creating complex devices with advanced functionality while maintaining a small form factor. A typical smartphone, for example, may use a multilayer PCB with 8 to 12 layers, each containing intricate circuit patterns. This design approach allows manufacturers to integrate processors, memory chips, wireless modules, and various sensors into a single, compact board. The result is a powerful device that fits comfortably in your pocket.Smaller PCB footprints save space
Modern PCB design techniques enable the creation of boards with smaller overall footprints. This space-saving capability is essential for the development of compact devices like wearables, IoT sensors, and miniature medical implants. By reducing the PCB size, designers can allocate more space for other critical components such as batteries or display screens. For instance, smartwatches rely on incredibly small PCBs to fit all necessary components within a wrist-worn form factor. These compact boards must support processors, memory, wireless connectivity, and various sensors while leaving room for a battery and display – all within a space smaller than a postage stamp.Thin PCBs fit sleek product enclosures
The thickness of PCBs has also been significantly reduced over the years, contributing to the sleek profiles of modern electronic devices. Thin PCBs, sometimes less than 0.4mm thick, allow product designers to create ultra-slim laptops, tablets, and flat-screen televisions without compromising on functionality or performance. These thin boards require precise manufacturing techniques and often utilize advanced materials to maintain structural integrity and electrical performance. The ICAPE Group specializes in producing such high-quality, thin PCBs that meet the demanding requirements of modern electronics manufacturers.PCBs provide reliable electrical connections
Beyond enabling compact designs, PCB technology is crucial for ensuring reliable electrical connections within electronic devices. The copper traces etched onto PCBs create stable pathways for electrical signals, significantly reducing the risk of short circuits or loose connections that can plague older wiring methods. PCBs offer several advantages in terms of electrical reliability:- Consistent impedance control for high-frequency applications
- Reduced electromagnetic interference (EMI) through proper trace routing
- Enhanced thermal management capabilities
- Improved signal integrity in complex circuits
PCB technology has revolutionized the reliability of electronic devices, enabling them to function flawlessly in environments that would have been unthinkable just a few decades ago.
PCB manufacturing offers design flexibility
The versatility of PCB technology provides engineers with unprecedented design flexibility. This adaptability allows for the creation of custom solutions tailored to specific application requirements, driving innovation across various industries.Various substrate materials for different applications
PCB manufacturers can choose from a wide range of substrate materials to meet specific performance needs. Common materials include:- FR-4 (flame retardant fiberglass-epoxy laminate) for general-purpose applications
- Polyimide for high-temperature environments
- PTFE (Teflon) for high-frequency RF applications
- Aluminum for improved heat dissipation
- Flexible substrates for dynamic or space-constrained applications
Copper traces routed for optimal performance
The ability to precisely control the routing of copper traces on PCBs is a key advantage of this technology. Engineers can design complex layouts that optimize signal paths, minimize crosstalk, and control impedance. This level of control is essential for high-speed digital circuits, RF designs, and sensitive analog applications. Advanced PCB design software allows for automated routing and signal integrity analysis, ensuring that trace layouts meet stringent performance requirements. This capability is particularly crucial in 5G telecommunications equipment, where signal integrity at high frequencies is paramount.Through-hole vias connect circuit layers
Through-hole vias are tiny plated holes that connect different layers of a multilayer PCB. These connections allow for complex three-dimensional circuit designs, enabling signals to traverse multiple layers efficiently. The strategic use of vias can significantly reduce board size and improve overall circuit performance. Modern PCB designs often employ advanced via technologies such as:- Blind vias: Connect outer layers to inner layers without going through the entire board
- Buried vias: Connect inner layers without being visible on the outer layers
- Microvias: Extremely small vias used in high-density interconnect (HDI) boards
Automated PCB assembly improves production efficiency
The standardized nature of PCB technology lends itself well to automated assembly processes, significantly enhancing production efficiency and consistency. This automation is crucial for meeting the high-volume demands of the modern electronics market while maintaining quality standards.Pick-and-place machines quickly mount components
Pick-and-place machines are the workhorses of PCB assembly lines. These highly accurate robots can place thousands of components per hour with precision that far exceeds human capabilities. The speed and accuracy of these machines enable the production of complex electronic devices at scale. Modern pick-and-place machines can handle components as small as0201
(0.6 mm × 0.3 mm) or even 01005
(0.4 mm × 0.2 mm) size, allowing for the creation of incredibly dense PCB assemblies. This capability is essential for producing miniature devices like hearing aids or smartwatches.
Automated soldering ensures consistent quality
Automated soldering techniques, such as wave soldering for through-hole components and reflow soldering for surface-mount devices, ensure consistent and reliable connections. These processes can precisely control temperature profiles and solder quantities, resulting in high-quality joints that are critical for device reliability. For example, in the automotive industry, where electronics must withstand extreme temperatures and constant vibration, automated soldering processes ensure that each connection meets stringent quality standards. This level of consistency is difficult, if not impossible, to achieve with manual soldering techniques.Optical inspection detects manufacturing defects
Automated optical inspection (AOI) systems play a crucial role in maintaining quality control during PCB assembly. These systems use high-resolution cameras and sophisticated image processing algorithms to detect defects such as misaligned components, solder bridges, or missing parts. AOI can inspect hundreds of boards per hour, identifying issues that might be missed by human inspectors. This rapid, accurate inspection process is essential for maintaining high production yields and ensuring the reliability of finished products.The combination of automated assembly and inspection processes has revolutionized PCB manufacturing, enabling the production of complex electronic devices with unprecedented speed and quality.