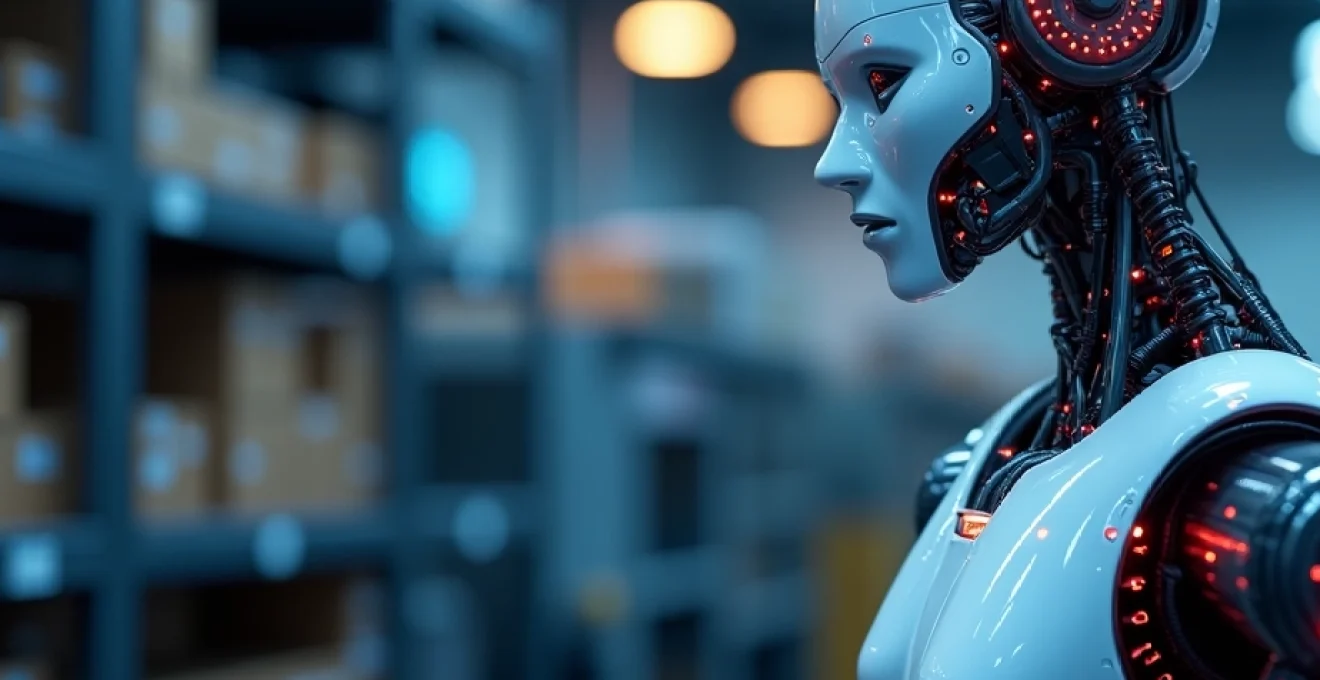
The industrial landscape is undergoing a profound transformation, driven by the rapid advancement of robotics technology. As manufacturers face increasing pressure to boost efficiency, improve quality, and reduce costs, robotic solutions are emerging as a game-changing force. From collaborative robots working alongside human operators to AI-powered systems capable of complex decision-making, the potential for robotics to revolutionize industrial operations is immense.
This shift towards automation is not just about replacing human workers; it's about augmenting human capabilities and creating new opportunities for innovation. By embracing robotics, companies can streamline their processes, enhance workplace safety, and unlock new levels of productivity. The question is no longer whether to adopt robotics, but how to integrate these technologies effectively to stay competitive in an increasingly automated world.
Industrial robotics: transforming manufacturing processes
Industrial robotics has come a long way since the introduction of the first robotic arm in the 1960s. Today's robots are faster, more precise, and more versatile than ever before. They're capable of performing a wide range of tasks, from welding and assembly to packaging and quality control. The impact of these machines on manufacturing processes has been nothing short of revolutionary.
One of the key advantages of industrial robots is their ability to work tirelessly, 24/7, without the need for breaks or shift changes. This continuous operation can significantly boost production output and efficiency. Moreover, robots can perform tasks with a level of precision and consistency that is difficult for humans to match, leading to higher quality products and reduced waste.
The integration of robotics into manufacturing processes also allows for greater flexibility. Modern robots can be quickly reprogrammed to handle different tasks or product variations, enabling manufacturers to respond swiftly to changing market demands. This adaptability is crucial in today's fast-paced business environment, where agility can mean the difference between success and failure.
Collaborative robots (cobots) in human-machine interaction
While traditional industrial robots are designed to work in isolation, a new generation of robots is changing the game. Collaborative robots, or cobots, are designed to work safely alongside human operators, combining the strength and precision of machines with the flexibility and problem-solving skills of humans. This human-machine collaboration is opening up new possibilities for industrial automation.
Universal Robots UR10e: enhancing workplace safety
The Universal Robots UR10e is a prime example of how cobots are enhancing workplace safety. This versatile robot arm can handle payloads of up to 10 kg and has a reach of 1300 mm, making it suitable for a wide range of applications. What sets the UR10e apart is its advanced safety features, including force sensing technology that allows it to detect obstacles and stop immediately if it comes into contact with a person.
By taking on repetitive or physically demanding tasks, the UR10e can reduce the risk of workplace injuries and improve ergonomics for human workers. Its ease of programming and quick setup time also make it an attractive option for small and medium-sized enterprises looking to dip their toes into automation.
FANUC CR-35iA: high-payload collaboration
For heavier-duty applications, the FANUC CR-35iA stands out as a powerful collaborative robot capable of handling payloads up to 35 kg. This cobot is designed to work in close proximity to humans without the need for safety fences, thanks to its soft rubber skin and force-limited sensors that detect contact with operators.
The CR-35iA's strength and reach make it ideal for tasks such as palletizing, machine tending, and heavy parts transfer. Its ability to take on these physically demanding jobs not only improves efficiency but also reduces the risk of repetitive strain injuries among human workers.
ABB YuMi: precision assembly applications
When it comes to precision assembly tasks, the ABB YuMi (short for "You and Me") sets a new standard for collaborative robotics. This dual-arm robot is designed to mimic human dexterity and is particularly well-suited for small parts assembly in industries such as electronics and consumer goods manufacturing.
YuMi's padded arms and advanced sensors ensure safe operation alongside humans, while its integrated vision system allows for precise part location and inspection. The robot's intuitive programming interface makes it easy for operators to teach new tasks, enabling rapid adaptation to changing production needs.
Rethink Robotics Sawyer: adaptive manufacturing solutions
Sawyer, developed by Rethink Robotics, represents a new breed of adaptive collaborative robots. Equipped with a high-resolution force-sensing system at each joint, Sawyer can perform delicate tasks with human-like sensitivity. This makes it particularly suitable for applications requiring fine motor skills, such as circuit board testing or precision part insertion.
What sets Sawyer apart is its ability to learn and adapt to its environment. Using advanced machine learning algorithms, Sawyer can improve its performance over time and even compensate for variations in part positioning or environmental conditions. This adaptability makes it an invaluable tool for manufacturers dealing with high-mix, low-volume production scenarios.
Advanced sensor integration for smart robotics
The effectiveness of modern industrial robots is greatly enhanced by the integration of advanced sensors. These sensors allow robots to perceive and interact with their environment in increasingly sophisticated ways, enabling them to perform more complex tasks and adapt to changing conditions.
LIDAR technology in autonomous mobile robots
LIDAR (Light Detection and Ranging) technology is revolutionizing the field of autonomous mobile robots (AMRs). By emitting laser pulses and measuring the time it takes for the light to reflect back, LIDAR sensors can create detailed 3D maps of their surroundings. This enables AMRs to navigate complex factory environments safely and efficiently, avoiding obstacles and optimizing their paths.
The integration of LIDAR in AMRs has significant implications for warehouse automation and material handling. These robots can now perform tasks such as inventory management, order picking, and even collaborative loading and unloading operations with minimal human intervention.
Machine vision systems for quality control
Machine vision systems are becoming increasingly sophisticated, allowing robots to perform complex inspection and quality control tasks with remarkable accuracy. These systems use high-resolution cameras and advanced image processing algorithms to detect defects, measure dimensions, and ensure product consistency.
In automotive manufacturing, for example, machine vision-equipped robots can inspect painted surfaces for imperfections invisible to the human eye. In the electronics industry, these systems can verify the correct placement of tiny components on circuit boards, ensuring product reliability and reducing the need for manual inspections.
Force/torque sensors in delicate assembly tasks
Force/torque sensors are enabling robots to perform delicate assembly tasks that previously required human touch. These sensors allow robots to "feel" the forces they're applying, enabling them to handle fragile components or perform precise fitting operations without causing damage.
In the aerospace industry, for example, force/torque sensors are used in robotic systems that assemble sensitive electronic components or perform precise bolt-tightening operations. The ability to control force application with high precision not only improves product quality but also reduces the risk of component damage during assembly.
IoT-enabled predictive maintenance for robotic systems
The Internet of Things (IoT) is transforming the way robotic systems are maintained and operated. By equipping robots with IoT-enabled sensors, manufacturers can continuously monitor their performance and predict potential failures before they occur. This predictive maintenance approach can significantly reduce downtime and extend the lifespan of robotic equipment.
IoT sensors can track parameters such as motor temperature, vibration levels, and power consumption. By analyzing this data in real-time, maintenance teams can schedule interventions at optimal times, minimizing disruption to production schedules and maximizing robot availability.
AI and machine learning in industrial robotics
Artificial Intelligence (AI) and Machine Learning (ML) are pushing the boundaries of what's possible in industrial robotics. These technologies are enabling robots to learn from experience, make decisions autonomously, and even improve their performance over time.
Deep reinforcement learning for adaptive robot control
Deep Reinforcement Learning (DRL) is a cutting-edge AI technique that allows robots to learn complex tasks through trial and error. By receiving feedback on their actions, robots can optimize their behavior to achieve specific goals. This approach is particularly useful for tasks that are difficult to program explicitly, such as grasping irregularly shaped objects or navigating dynamic environments.
In automotive manufacturing, DRL is being used to teach robots how to perform complex assembly tasks that require dexterity and adaptability. As the robot practices, it learns to adjust its movements based on variations in part positioning or assembly conditions, leading to more robust and flexible automation solutions.
Computer vision algorithms for object recognition
Advanced computer vision algorithms, powered by deep learning, are dramatically improving robots' ability to recognize and interact with objects. These systems can identify items based on their shape, color, or texture, even in cluttered or variable lighting conditions. This capability is crucial for applications such as bin picking, where robots need to locate and grasp specific parts from a mixed assortment.
In the logistics industry, AI-powered vision systems are enabling robots to sort packages of various sizes and shapes with high accuracy. This technology is also being applied in recycling facilities, where robots can identify and sort different types of materials, improving the efficiency and effectiveness of recycling processes.
Natural Language Processing in human-robot interfaces
Natural Language Processing (NLP) is making it easier for humans to interact with and program robots. Instead of complex coding, operators can use natural language commands to instruct robots or query their status. This technology is particularly valuable in collaborative environments, where it can facilitate smoother communication between human workers and their robotic counterparts.
For example, in a manufacturing setting, a worker might say, "Robot, please bring me a new set of screws," and the NLP-enabled robot would understand and execute the request. This intuitive interface reduces the learning curve for working with robots and can improve overall productivity in human-robot collaborative environments.
Generative AI for robotic path planning optimization
Generative AI techniques, such as those used in creating realistic images or text, are now being applied to optimize robotic path planning. These algorithms can generate and evaluate thousands of potential paths, considering factors such as collision avoidance, energy efficiency, and cycle time optimization.
In complex manufacturing environments with multiple robots working in close proximity, generative AI can help coordinate movements to maximize efficiency while ensuring safety. This technology is particularly valuable in industries such as automotive or aerospace manufacturing, where optimizing robot movements can lead to significant improvements in production throughput.
End-of-arm tooling (EOAT) innovations
The effectiveness of industrial robots is greatly influenced by their end-of-arm tooling (EOAT). Recent innovations in EOAT design are expanding the range of tasks that robots can perform and improving their overall efficiency. From advanced grippers to multi-functional tools, these developments are pushing the boundaries of robotic capabilities.
One notable trend is the development of adaptive grippers that can handle a wide range of object sizes and shapes. These grippers use sensors and flexible materials to adjust their grip force and shape, allowing them to securely handle delicate items or oddly shaped parts without the need for tool changes. This versatility is particularly valuable in industries with high product variability, such as e-commerce fulfillment or mixed-model assembly lines.
Another exciting development is the integration of 3D printing technology in EOAT design. Custom-designed, 3D-printed tools can be quickly produced to meet specific application requirements, reducing lead times and costs associated with traditional tooling methods. This approach also allows for the creation of complex geometries that would be difficult or impossible to achieve with conventional manufacturing techniques.
Robotic process automation (RPA) in manufacturing
While physical robots are transforming the factory floor, Robotic Process Automation (RPA) is revolutionizing the digital side of manufacturing operations. RPA software "robots" can automate repetitive, rule-based tasks across various business processes, from order processing to quality control documentation.
In production planning, RPA can automatically gather data from multiple systems, analyze production schedules, and generate optimized plans based on predefined rules. This not only saves time but also reduces the risk of human error in complex planning processes. Similarly, in supply chain management, RPA can monitor inventory levels, generate purchase orders, and even communicate with suppliers automatically, ensuring smooth material flow and reducing stockouts.
The integration of RPA with physical robotics systems is creating new opportunities for end-to-end automation in manufacturing. For example, an RPA system could process customer orders, automatically generate production schedules, and then communicate these schedules to shop floor robots for execution. This seamless integration of digital and physical automation has the potential to dramatically improve operational efficiency and responsiveness to customer demands.
As industrial robotics continues to evolve, the possibilities for improving manufacturing processes seem limitless. From collaborative robots that enhance human capabilities to AI-powered systems that can learn and adapt, the robotics revolution is well underway. By embracing these technologies and integrating them thoughtfully into their operations, manufacturers can position themselves at the forefront of industrial innovation, ready to meet the challenges and opportunities of the future.